Spis treści
Co to jest manometr?
Manometr to niezwykle istotne narzędzie, które mierzy ciśnienie cieczy lub gazu w zamkniętej przestrzeni. Jego kluczowa rola polega na pomiarze ciśnienia w odniesieniu do ciśnienia otoczenia, zazwyczaj atmosferycznego. Te urządzenia znajdują zastosowanie w:
- systemach hydraulicznych,
- różnorodnych instalacjach przemysłowych,
- branżach takich jak motoryzacja,
- przemysł chemiczny,
- gazowy.
Dzięki manometrom można precyzyjnie określić ciśnienie, co jest istotne w takich branżach jak motoryzacja, przemysł chemiczny czy gazowy. Pozwalają one na bieżąco monitorować ciśnienie oleju hydraulicznego, gazu ziemnego oraz powietrza w różnorodnych systemach pneumatycznych, co przekłada się na bezpieczeństwo i efektywność pracy urządzeń. W szczególności w systemach hydraulicznych manometry są nieocenione w kontrolowaniu siły, co jest kluczowe dla optymalnego funkcjonowania całego systemu. Umożliwiają one także wcześniejsze wykrywanie potencjalnych awarii oraz nieprawidłowości, co nadaje większą sprawność w działaniach naprawczych oraz redukuje ryzyko nieprzewidzianych usterek. Co więcej, są to urządzenia niezwykle wszechstronne, które mogą być wykorzystywane w różnych warunkach oraz w wielu sektorach przemysłowych. Dzięki temu manometry odgrywają fundamentalną rolę w rozmaitych procesach technologicznych.
Do czego służy manometr?
Manometr to urządzenie, które służy do pomiaru ciśnienia cieczy i gazów w stosunku do ciśnienia atmosferycznego. Dzięki niemu możemy skutecznie monitorować ciśnienie w wodzie oraz gazach w wielu instalacjach, takich jak:
- hydraulika,
- ciepłownictwo,
- gazownictwo.
Umożliwia on diagnozowanie usterek oraz kontrolowanie ciśnienia roboczego w różnych procesach. W hydraulice manometr pełni kluczową rolę w ocenie ciśnienia oleju, co bezpośrednio wpływa na bezpieczeństwo i efektywność działania maszyn. Ponadto, pozwala na pomiar ciśnienia wody w rurach oraz ocenę wydajności pomp ciepła, co jest istotne w kontekście systemów grzewczych. Manometry hydrauliczne i pneumatyczne oferują dokładne dane, które są niezmiernie cenne w procesach przemysłowych, a ich zastosowanie przyczynia się do optymalizacji procesów oraz wcześniejszego wykrywania potencjalnych problemów. Z tego względu manometr staje się niezastąpionym elementem w każdym systemie, gdzie precyzyjne pomiary ciśnienia są kluczowe dla sprawnego działania urządzeń oraz technologii.
Jak działa manometr?
Manometr działa na zasadzie deformacji elastycznego elementu sprężystego pod wpływem ciśnienia cieczy lub gazu. W manometrach wyposażonych w rurkę Bourdona, ciśnienie prostuje zakrzywioną rurkę, co uruchamia wskaźnik na skali pomiarowej. Z kolei w manometrach membranowych, reakcja membrany na działające ciśnienie prowadzi do jej deformacji. Wartości pomiarowe są uzależnione od przemieszczenia sprężystego elementu.
Co więcej, niektóre manometry stosują płyny, na przykład glicerynę, co znacząco zwiększa ich odporność na wibracje oraz podnosi dokładność pomiarów w trudnych warunkach, szczególnie przy wysokim ciśnieniu. Manometry znalazły szerokie zastosowanie w różnych dziedzinach, takich jak:
- przemysł,
- motoryzacja,
- hydraulika,
- gdzie precyzyjne pomiary ciśnienia odgrywają kluczową rolę w efektywności systemów.
Ich dostępność w wielu wersjach, od niskociśnieniowych po wysokociśnieniowe, czyni je niezwykle wszechstronnymi narzędziami pomiarowymi.
Jakie są główne typy manometrów?
Wśród najpopularniejszych typów manometrów możemy wyróżnić:
- manometry mechaniczne, takie jak te z rurką Bourdona, które działają na zasadzie deformacji sprężystych elementów pod wpływem ciśnienia,
- manometry membranowe, w których nacisk wywierany na membranę prowadzi do jej odkształcenia,
- manometry puszkowe, które zmieniają kształt specjalnej puszki w odpowiedzi na zmiany ciśnienia,
- manometry hydrostatyczne, stosujące różnice wysokości słupków cieczy do pomiaru ciśnienia, idealne do wykorzystania w systemach wodnych,
- manometry elektroniczne, znane też jako ciśnieniomierze elektryczne, które stosują przetworniki ciśnienia, przekształcając ciśnienie na sygnały elektryczne.
Ta technologia pozwala na szybsze i bardziej precyzyjne pomiary oraz efektywne zapisywanie danych. Każdy z wymienionych typów ma swoje specyficzne zastosowania. Na przykład, manometry z rurką Bourdona cieszą się popularnością w przemyśle motoryzacyjnym, a manometry elektroniczne często wykorzystuje się w zaawansowanych systemach monitorowania.
W kontekście pomiaru ciśnienia bezwzględnego, manometry mogą mieć różnorodne dodatkowe funkcje, takie jak:
- wskazywanie wartości minimalnych i maksymalnych,
- przetwarzanie sygnału w czasie rzeczywistym.
Dlatego wybór odpowiedniego manometru jest niezwykle istotny dla uzyskania dokładnych pomiarów w różnych zastosowaniach. Warto zatem dostosować go do konkretnych potrzeb oraz warunków, w jakich będzie używany.
Jakie są różnice między manometrem membranowym a rurką Bourdona?
Manometr membranowy i manometr z rurką Bourdona różnią się zarówno konstrukcją, jak i zastosowaniami. W przypadku manometru membranowego mamy do czynienia z elastyczną membraną, która deformuje się pod wpływem ciśnienia cieczy lub gazu. Sprawia to, że jest on idealny do pomiarów w obecności:
- agresywnych substancji,
- wilgotnych środowisk,
- wysokiej precyzji.
Z kolei manometr z rurką Bourdona składa się z zakrzywionej rurki, która prostuje się w miarę wzrostu ciśnienia, co przesuwa wskaźnik na skali. Ten typ urządzenia jest skuteczny w mierzeniu ciśnienia:
- gazów,
- cieczy,
- zwłaszcza w mniej wymagających zastosowaniach przemysłowych.
Choć manometry Bourdona mają szeroki zakres pomiarowy, nie zawsze są odpowiednie do racy z bardziej agresywnymi materiałami. Warto więc przy wyborze pomiędzy manometrem membranowym a Bourdona kierować się specyfiką pomiaru oraz rodzajem medium. Manometr membranowy doskonale sprawdzi się w trudniejszych warunkach, podczas gdy jego odpowiednik z rurką Bourdona jest częściej wykorzystywany w typowych aplikacjach przemysłowych.
Jakie zalety manometrów cyfrowych w porównaniu do tradycyjnych?
Manometry cyfrowe mają liczne zalety w porównaniu do tradycyjnych rozwiązań, co sprawia, że stają się coraz bardziej popularnym wyborem w różnych dziedzinach. Przede wszystkim zapewniają one wyjątkową precyzję pomiarów, co jest niezwykle istotne w przypadku technologii wymagających dokładności. Dzięki wbudowanym przetwornikom ciśnienia, pomiary są błyskawicznie przekształcane w sygnały elektryczne, co eliminuje błędy odczytu, które mogą wystąpić przy użyciu tradycyjnych skal.
Kolejnym plusem cyfrowych manometrów jest ich intuicyjność. Wyraźne wyświetlacze gwarantują szybki podgląd wartości ciśnienia, co znacząco redukuje ryzyko pomyłek. Warto również zauważyć, że wiele modeli umożliwia rejestrowanie danych, co sprzyja monitorowaniu ciśnienia w trybie rzeczywistym oraz dokładnej dokumentacji pomiarów.
Integracja z systemami monitorującymi to kolejny etap, który zwiększa funkcjonalność manometrów cyfrowych. Dzięki możliwości podłączenia do komputerów, analiza danych staje się prostsza, co znacząco podnosi efektywność zarządzania procesami przemysłowymi. Dodatkowo, manometry cyfrowe oferują wiele interesujących funkcji, w tym ustawienia alarmowe, które informują użytkownika o przekroczeniu określonych wartości ciśnienia. Takie rozwiązania nie tylko zwiększają bezpieczeństwo, ale również umożliwiają szybką reakcję na ewentualne zagrożenia.
W skrócie, manometry cyfrowe to nowoczesne, precyzyjne i wielofunkcyjne urządzenia do pomiaru ciśnienia, które w nowoczesnych zastosowaniach przemysłowych z powodzeniem zastępują tradycyjne manometry mechaniczne.
Jakie rodzaje ciśnienia można mierzyć za pomocą manometru?
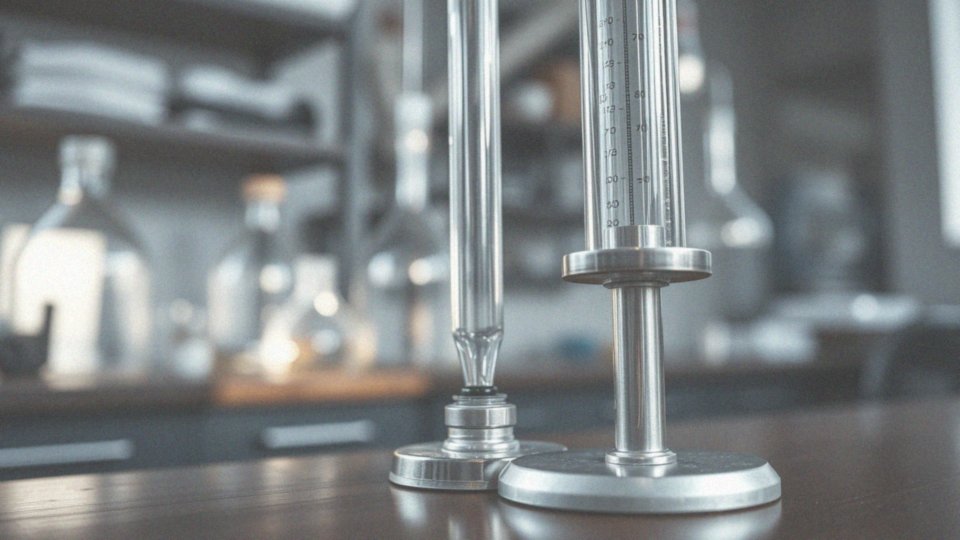
Manometr to urządzenie służące do pomiaru różnych rodzajów ciśnienia. To narzędzie jest naprawdę wszechstronne. Najważniejszym z pomiarów jest ciśnienie bezwzględne, które odnosi się do próżni i pozwala ustalić całkowite ciśnienie w danym miejscu, pomijając wpływ atmosfery. Na przykład, w środowisku laboratoryjnym ciśnienie w próżni mierzy się właśnie w kategoriach ciśnienia bezwzględnego.
Innym istotnym rodzajem pomiaru jest ciśnienie względne, które określa się w odniesieniu do ciśnienia atmosferycznego. Tego rodzaju pomiary mają znaczenie w wielu zastosowaniach, na przykład w hydraulice, gdzie ważne jest, aby monitorować ciśnienie w kontekście otoczenia. Dzięki temu możemy zmniejszyć ryzyko uszkodzenia urządzeń oraz zwiększyć ich efektywność.
Kolejny, interesujący typ to ciśnienie różnicowe. Mierzy ono różnice ciśnienia między dwoma punktami w systemie, co jest kluczowe dla oceny wydajności filtrów i innych elementów w układach hydraulicznych oraz pneumatycznych. Takie pomiary mają oczywisty wpływ na ogólną kondycję i efektywność całego systemu.
Manometry znajdują zastosowanie także w pomiarach ciśnienia na różnych wysokościach, co jest szczególnie istotne w hydraulice czy przy użyciu pomp. Właściwe zrozumienie różnic poziomów może znacząco wpłynąć na wydajność. Do tych pomiarów używa się różnych jednostek, takich jak:
- pascale (Pa),
- atmosfera (atm),
- milimetry słupa rtęci (mmHg).
Dlatego manometry odgrywają kluczową rolę w branżach takich jak przemysł, motoryzacja i medycyna.
Jak monitorować ciśnienie przy użyciu manometru?
Aby skutecznie monitorować ciśnienie za pomocą manometru, warto przestrzegać kilku ważnych kroków:
- upewnij się, że urządzenie jest prawidłowo zainstalowane w systemie, co jest kluczowe dla uzyskania dokładnych pomiarów,
- przeprowadź kontrolę stanu manometru, by zidentyfikować ewentualne uszkodzenia mechaniczne lub wycieki,
- regularnie sprawdzaj wskazania manometru, aby na bieżąco porównywać wyniki z oczekiwanym ciśnieniem roboczym,
- monitorowanie powinno odbywać się w ustalonych odstępach czasowych, co zmniejsza ryzyko awarii systemu,
- wdroż odpowiednie procedury diagnostyczne w przypadku zauważenia jakiejkolwiek nieprawidłowości,
- ponownie weryfikuj odczyty, aby zyskać pewność co do ich prawidłowości.
Zespół odpowiedzialny za analizę danych ma szansę na szybsze identyfikowanie usterek oraz sprawniejsze zarządzanie całym systemem. Dzięki regularnemu monitorowaniu ciśnienia technicy mogą na bieżąco zajmować się problemami, co przekłada się na minimalizację ryzyka wypadków w systemach HVAC/R oraz innych instalacjach. Precyzyjny pomiar ciśnienia ma kluczowe znaczenie dla bezpieczeństwa i efektywności działania, a odpowiednie zarządzanie manometrami sprawia, że stają się one niezastąpionymi narzędziami w procesach przemysłowych.
Jak instalować manometr prawidłowo?
Aby właściwie zamontować manometr, warto pamiętać o kilku istotnych zasadach:
- należy odpowiednio dopasować manometr do zakresu ciśnienia oraz rodzaju medium,
- jego orientacja ma ogromne znaczenie, ponieważ ułatwia późniejszy odczyt wskazań,
- instalacja powinna być przeprowadzana w miejscach, w których wibracje są minimalne,
- kluczowe jest staranne zabezpieczenie połączeń, aby uniknąć ewentualnych wycieków,
- właściwe użycie uszczelnień i śrub zapewni szczelność całej konstrukcji,
- dobrze jest sprawdzić manometr pod kątem ewentualnych uszkodzeń przed montażem,
- regularne kontrolowanie wskazań po zakończeniu instalacji jest niezbędne.
Dzięki tym działaniom możemy mieć pewność, że manometr pracuje w oczekiwanym zakresie, co z kolei wpływa na optymalizację procesów w zakładach przemysłowych oraz innych systemach.
Jak wygląda proces kalibracji manometru?
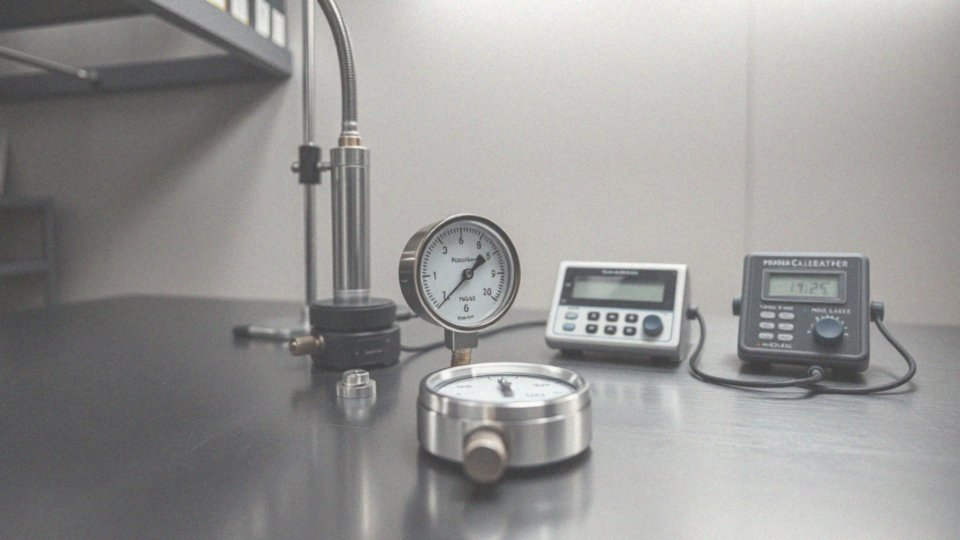
Kalibracja manometru to niezwykle ważny proces, który zapewnia precyzyjność pomiarów ciśnienia. Obejmuje ona porównywanie wyników z manometru z pomiarami uzyskanymi za pomocą wzorcowych urządzeń. Do tego celu wykorzystuje się sprzęt, który charakteryzuje się znaną i dokładną wartością ciśnienia. W przypadku wykrycia jakichkolwiek odchyleń po dokonaniu pomiarów, wprowadza się odpowiednie korekty, co pozwala na dokładne pomiary.
Regularne kalibrowanie jest kluczowe dla unikania błędów, które mogą prowadzić do poważnych konsekwencji, szczególnie w systemach hydraulicznych i pneumatycznych, gdzie precyzyjne dane są niezbędne dla bezpieczeństwa i efektywności działania. Cały proces kalibracji wymaga zespołu przeszkolonego personelu oraz odpowiednich warunków laboratoryjnych, co zapewnia wiarygodność wyników.
Należy również pamiętać, że czynniki takie jak temperatura otoczenia czy ciśnienie atmosferyczne mają wpływ na dokładność manometru, dlatego powinny być brane pod uwagę podczas kalibracji. Przy odpowiedniej kalibracji można optymalizować różne procesy przemysłowe. Manometry znajdują zastosowanie w wielu branżach, od kontrolowania ciśnienia w systemach pneumatycznych, aż po hydrauliczne i chemiczne.
Jakie czynniki wpływają na dokładność pomiaru manometru?
Dokładność pomiarów manometru jest uzależniona od kilku kluczowych czynników. Przede wszystkim, jakość samego urządzenia ma znaczący wpływ na jego precyzję. Użycie materiałów wysokiej klasy oraz staranność w procesie produkcji znacznie zwiększają niezawodność manometru.
- warunki, w jakich pracuje urządzenie;
- temperatura oraz wibracje mogą wpływać na dokładność wyników;
- niewłaściwy montaż manometru prowadzi do błędnych wskazań;
- właściwa instrukcja producenta dotycząca instalacji i orientacji urządzenia;
- regularna kalibracja manometru, aby uniknąć narastających błędów pomiarowych.
Również design oraz lokalizacja manometru mają znaczenie dla uzyskiwanych danych, zwłaszcza gdy chodzi o medium, w którym jest stosowany. W przypadku substancji chemicznie agresywnych ważne jest, aby materiały wykorzystane do produkcji były odporne na korozję, co pomoże uniknąć błędnych pomiarów. Zrozumienie tych kluczowych aspektów jest fundamentalne dla zapewnienia rzetelności pomiarów ciśnienia w różnych zastosowaniach przemysłowych.
Jakie problemy mogą wystąpić podczas użytkowania manometru?
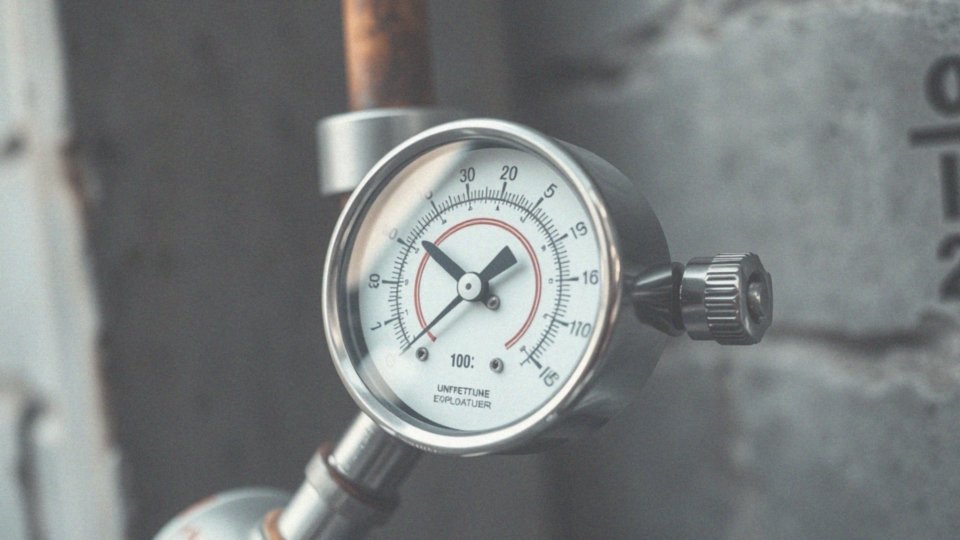
Kiedy korzystamy z manometru, musimy być świadomi różnych problemów, które mogą wpłynąć na dokładność naszych pomiarów ciśnienia i bezpieczeństwo całego systemu. Często napotykane trudności związane są z:
- uszkodzeniami mechanicznymi, które najczęściej pojawiają się w wyniku nieprawidłowej instalacji lub narażenia na wibracje,
- zanieczyszczeniem medium pomiarowego, gdzie obecność cząstek stałych czy osadów, na przykład w wodzie lub gazach, może znacząco wpłynąć na precyzję pomiarów,
- rozkalibrowaniem manometru, które może wystąpić podczas użytkowania. Różnice w temperaturze, wahania ciśnienia oraz czas eksploatacji mają bezpośredni wpływ na dokładność odczytów,
- wyciekami w systemie, które są poważnym zagrożeniem, zwłaszcza że wysokie ciśnienie robocze może prowadzić do wybuchów lub uszkodzeń sprzętu,
- zbyt niskim ciśnieniem, które może sugerować konieczność przeprowadzenia prac konserwacyjnych lub wskazywać na inne problemy w instalacji.
Ważne jest, aby na bieżąco monitorować stan manometru i szybko reagować na pojawiające się nieprawidłowości. Dbałość o te aspekty jest kluczowa dla zapewnienia efektywności oraz bezpieczeństwa w pracy z systemami pomiarowymi.
Jakie są zastosowania manometrów w różnych branżach?
Manometry znajdują szerokie zastosowanie w różnych sektorach, gdzie dokładny pomiar ciśnienia jest niezwykle ważny. Oto przykłady ich zastosowania:
- przemysł chemiczny – monitorują ciśnienie substancji agresywnych, co zapewnia bezpieczeństwo operacji i redukuje ryzyko awarii,
- automatyka przemysłowa – kluczowe dla kontroli ciśnienia instalacji hydraulicznych, co ma istotny wpływ na efektywność działania maszyn i urządzeń,
- sektor energetyczny – pozwalają na pomiar ciśnienia w instalacjach gazowych, co jest niezbędne dla zachowania stabilności sieci energetycznej,
- cieplownictwo – ułatwiają kontrolowanie ciśnienia, co umożliwia regulację wydajności pomp ciepła oraz utrzymanie optymalnych warunków grzewczych,
- medycyna – monitorują ciśnienie w aparaturze medycznej, co jest kluczowe dla bezpieczeństwa i zdrowia pacjentów,
- budownictwo – manometry pomocnicze współpracują z różnorodnymi urządzeniami, kontrolując ciśnienia robocze sprężarek powietrza oraz systemów hydraulicznych.
Dzięki swojej wszechstronności, manometry stały się nieodłącznym elementem efektywnego zarządzania i nadzoru w różnych branżach, przyczyniając się do zwiększenia bezpieczeństwa oraz optymalizacji procesów przemysłowych.